section-24ca95c
END MES
section-bd18706
Highlights
- Operational excellence
- Supply chain efficiency
- Continuous improvement and sustainability
- Real-time monitoring of processes and performance
- Efficiency and resource utilization optimization
- Increased labor productivity
- Reduced production costs
- Machine comparisons
- Alternative material and equipment management
- Supervisory control
- Detection and improvement of production bottlenecks
- Digital twin of the factory
- Minimizing human-related errors
- Raw material usage optimization
- Product controls and traceability
- Reduction of rework, errors, destruction and scrap
- Adaptable business intelligence
- Administrator consoles (Dashboard)
- Integration with different ERPs
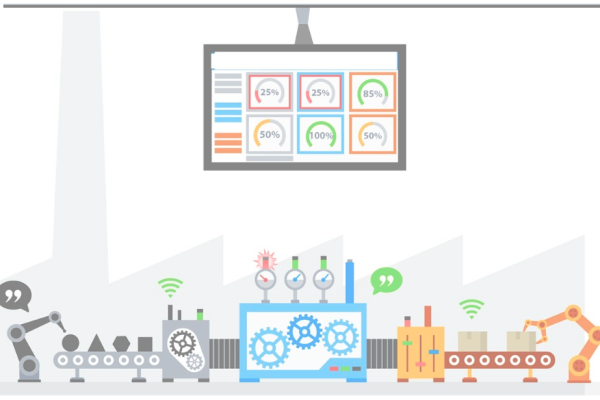
section-503fad7
The MES system controls production processes at the factory level. It receives all production information from robots, machines, sensors, production lines and operators in real time, and is integrated into enterprise resource planning (ERP) software, if any. Thus, production efficiency increases and improvements can be made in production processes. Product deliveries can be made with quality, on time and at affordable costs.
END MES operates in a controlled manner without the need for human intervention at many different stages of production operations, providing a fast production flow.
END MES, has the ability to work with different ERPs (enterprise resource planning software). The integration can increase operational clarity and strengthen the ability of organizations to monitor and improve performance according to their business plans.
section-ae98571
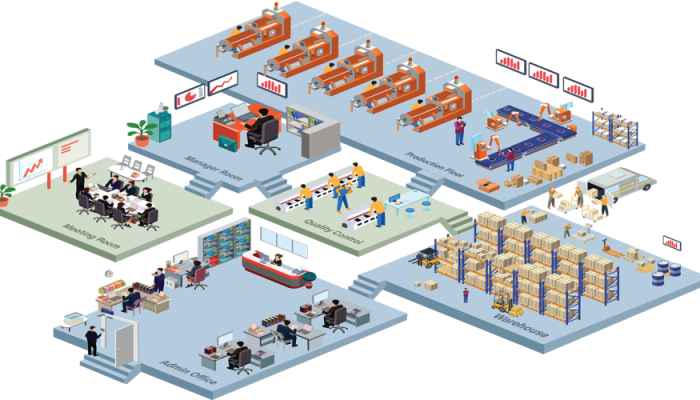
section-a676be8
END MES and END Energy Integration
Thanks to the integration, data from analyzers and production are collected at a single point, and the changes that occur are continuously recorded and monitored.
END Energy integration will enable the creation of an infrastructure compatible with the ISO 50001 Energy Management System, understanding the base energy consumption of the facility, creating action plans, setting targets to reduce consumption and creating energy performance indicators, and identifying, prioritizing and recording improvement opportunities to improve energy performance.
After this integration, which is the first stage of optimizing production times and energy consumption, it is possible to create the structure that will be used to estimate production times and energy consumption amounts using data mining and machine learning algorithms.