section-ae98571
Digital Twin in Production
The concept of a digital twin refers to the creation of a digital model of a physical asset (e.g. product, process, or system) and its real-time monitoring. This is the creation of a virtual copy of a physical asset in a computer-based environment. Digital twins are used to better understand, optimize, and manage complex systems.
In manufacturing, digital twins are used to monitor, analyze, and improve manufacturing processes. By creating a digital copy of a physical production line, factory, or product, data is collected and analyzed in real time. This data can be used to monitor the performance of the manufacturing process, detect errors, increase efficiency, and optimize processes.
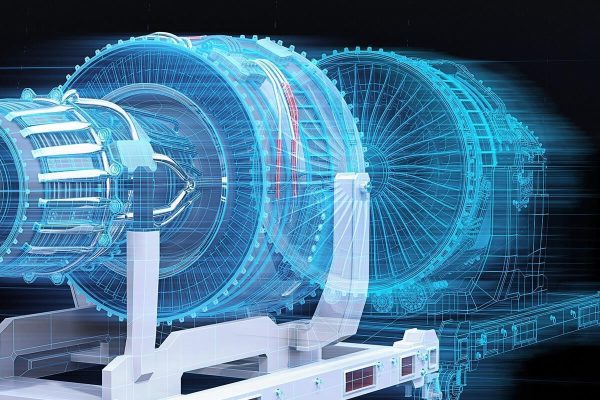
Digital twins create a virtual representation of the production process by collecting real-time data through sensors and other automation technologies. This allows monitoring and analysis of information about the production process. For example, if a failure occurs on the production line, this problem can be detected on the digital twin and quickly intervened.
Digital twins are also used for simulation and scenario analysis. Digital twins can be used to evaluate how production processes will react under different scenarios, what an optimized production flow would be like. This is an important tool for better planning production processes, using resources effectively, and increasing production efficiency.
As a result, digital twins in manufacturing are a powerful tool used to monitor, analyze, optimize, and improve processes. This can increase production efficiency, improve quality, and reduce costs.